As a plant we are continually looking to improve our product, processes, system and services. Through continuous improvement, we can strengthen product quality, lower production costs and increase throughput – all while decreasing labor costs.
This past summer, orders through our patio door department ramped up very quickly and it was difficult to adequately staff the team and acquire the materials. Challenges were felt from the factory floor to the field. It quickly became a perfect opportunity to apply the continuous improvement tools we have learned.
Customers wanted more volume than we could produce. We needed to figure out a way to manufacture more doors in the same amount of time, without sacrificing quality, safety, or on-time to the customer.
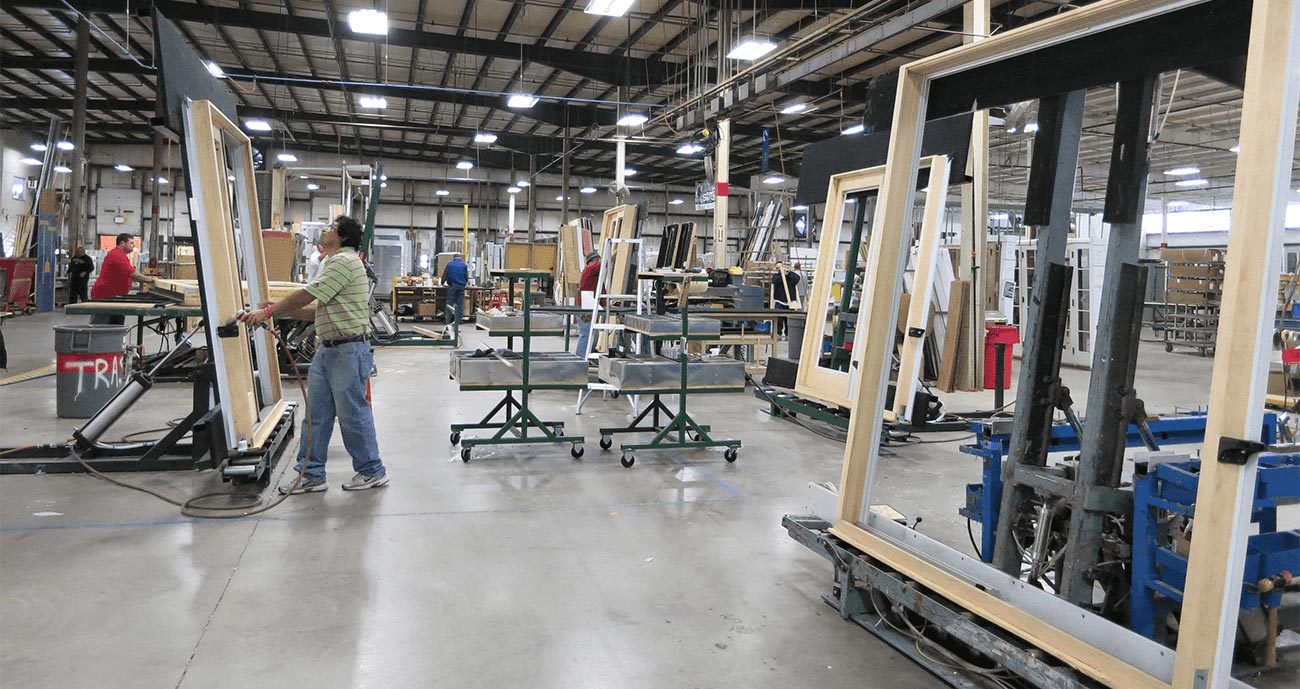
A multi-plant team was formed to attack the issue and improve the situation in a short period of time. The team spent a week and identified multiple items that needed to be addressed to reach our future goal.
We discovered simple changes that could be implemented quickly and removed unnecessary clutter and equipment. We executed significant changes to the equipment layout as well as some alterations to the overall process.
The team came away with 45 tasks that need to be completed within 8 weeks. The work of this team resulted in a patio door department with nearly twice the capacity of one year ago.