No, we’re not referring to a new dance here. (Although, the people in our facilities group may have felt like their heads were spinning these past few months.) Windsor’s West Des Moines Operations Team spent most of the summer preparing for the production of our new Pinnacle Select product line. The manufacturing floor has been rearranged, new equipment was purchased and new processes were set in place as we prepared an efficient start-up of this high-end product line.
Pinnacle Select products use a completely re-designed sash within the existing Pinnacle frame. The Select sash profile is larger than the standard Pinnacle sash, allowing for new features and providing even better performance. The new sash was designed to accommodate an optional push-out style hardware unit, as well as an optional retractable screen. An important benefit of this wider sash is higher design pressure performance.
The Select sash could not be produced on our current equipment. Therefore, a new assembly area was required. Equipment and materials were moved and condensed to create space. An area next to the current casement line was designated for this process. The frame has only small variations and can therefore be produced on the current equipment.
Along with several small fixture and tooling changes, there were three primary pieces of equipment that were designed and built for this production: a framing machine, a glazing machine, and a hardware pre-drilling machine. Each piece of equipment had to be fabricated and assembled on site and then qualified for quality and safety.
The final step was to execute several pilot production runs. These tests simulate productions for all sizes and configurations of the product. Pilot runs verify that correct information is being relayed to the shop floor and insures proper operation and accurate assembly of the units.
This process has been very time and labor intensive, but perseverance has paid off. Windsor is ready to manufacture the Pinnacle Select product line.
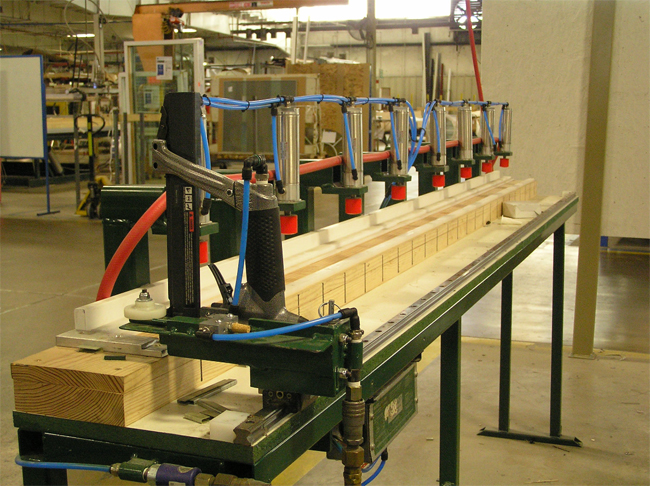
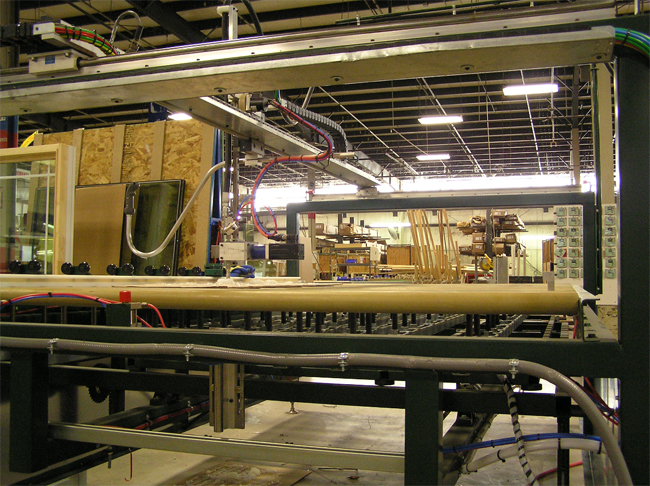
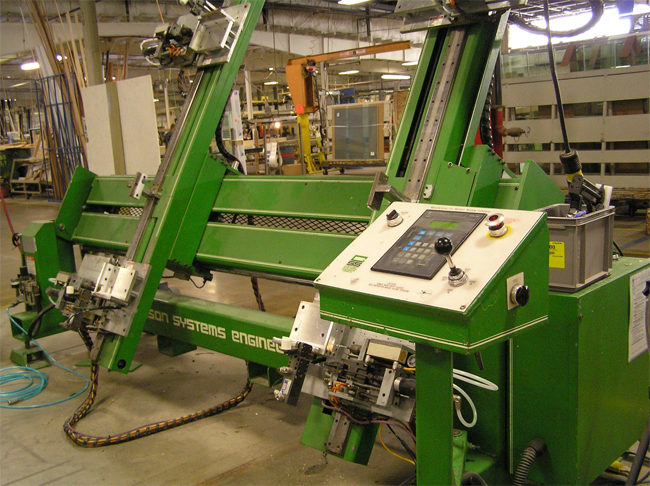